ULTRASHIELD® VS. CONVENTIONAL DECKING
STAINS
Step 1: Stain with black ink | |
|
|
Step 2: Wipe out half of the ink | |
![]() |
![]() |
Step 3: Wash off by water | |
![]() |
![]() |
Last Step: Dry and see the result | |
![]() |
![]() |
SCRATCHES
- Use 1mm needle
- Test scratch damage under 8N-20N pressure
- Test standard: FLTM BO 162-01
|
|
|
|
|
|
ABRASIONS
- Testing: 750g Weight, 60 turn/min, 1000 turns
- Test Standard: ASTM D4060
Original | |
|
|
Scratch mark and the wore off powder weight after test | |
|
|
UV
QUV chamber test up to 3000 hours
Observation & record in every 500 hours
|
|
|
|
|
|
|
BOILING
- Step 1: Put the test samples in the container (the water level needs to cover the samples by at least 5 mm or more)
- Step 2: Turn on the heating plate to 100 degrees Celsius and record/observe every 2 hours
- Step 3: Samples need to be taken out every day and the duration should be recorded. The duration is recorded after the temperature of the hot plate reaches 100 degrees Celsius
- Step 4: Repeat procedure 1-3 on the second day
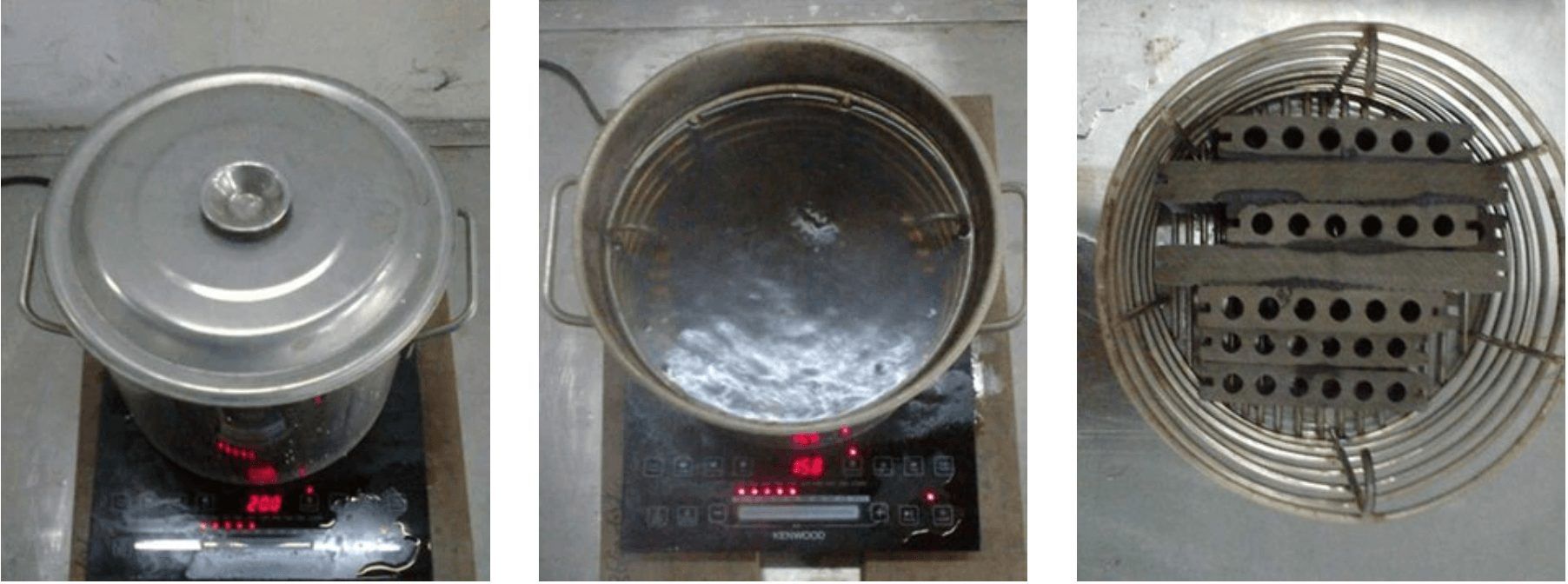